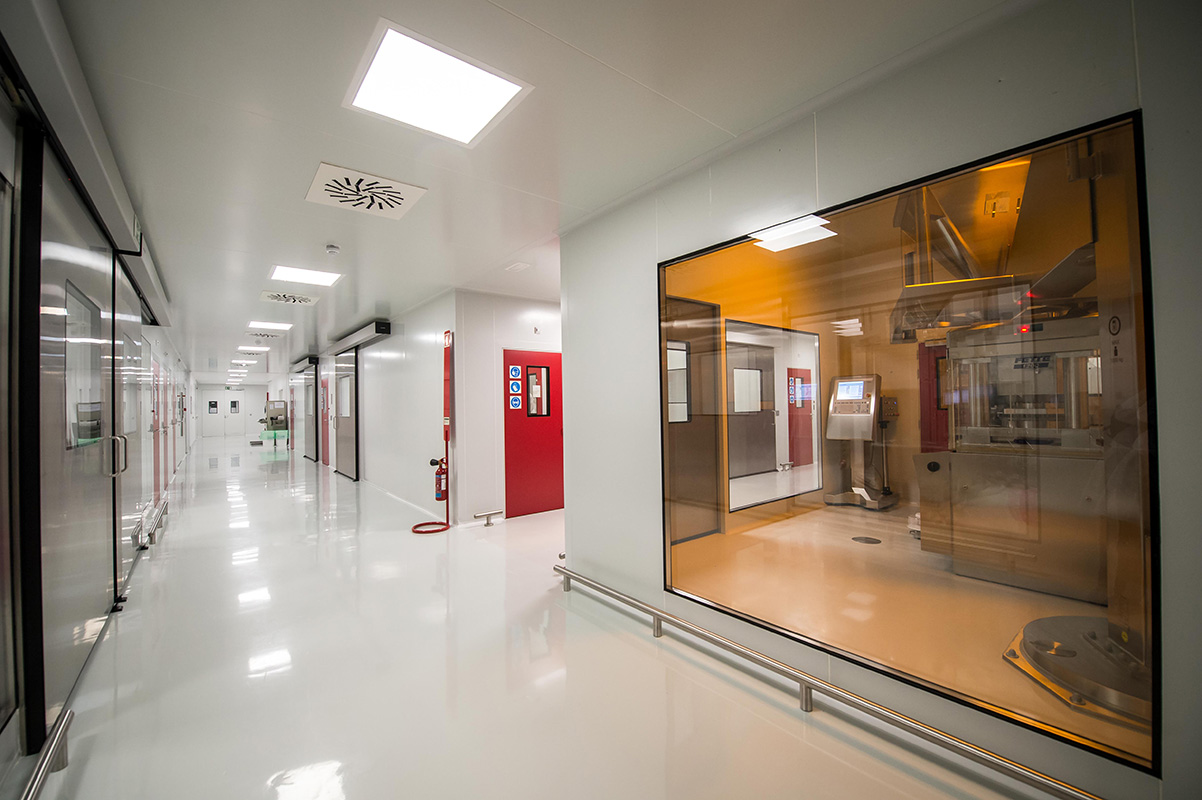
Oral Solids
Production
Our solids production area has been successively upgraded and equipped with state-of-the-art production technologies.
Our facilities can cover a wide range of batch sizes, typically from 30 kg to 700 kg.
Our facilities meet and exceed the applicable GMP standards. Each production room has people and/or material antechambers, sophisticated HVAC systems designed for ISO8 clean rooms, differential pressure cascades and other applicable specifications.
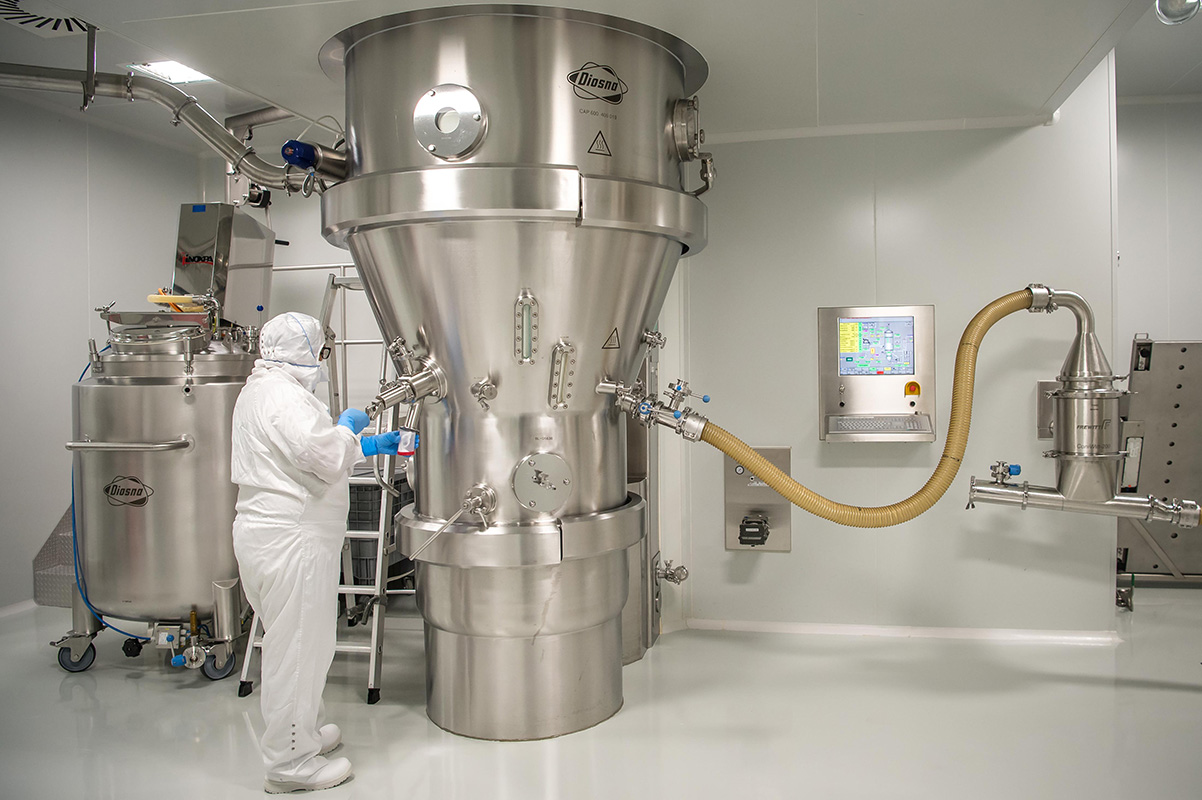
Oral Solids
Production
Mixing and granulation processes comprise low-shear and high-shear technologies, followed by static or fluidized bed dryers (FBD) depending on the process requirements.
Fluid Bed Top Spray Granulation Systems as well as bottom-spray pelletization by Würster system are both available in 600-litre FBD units.
The final mixture is obtained in a set of IBCs with working range from 120 to 1400 litres.
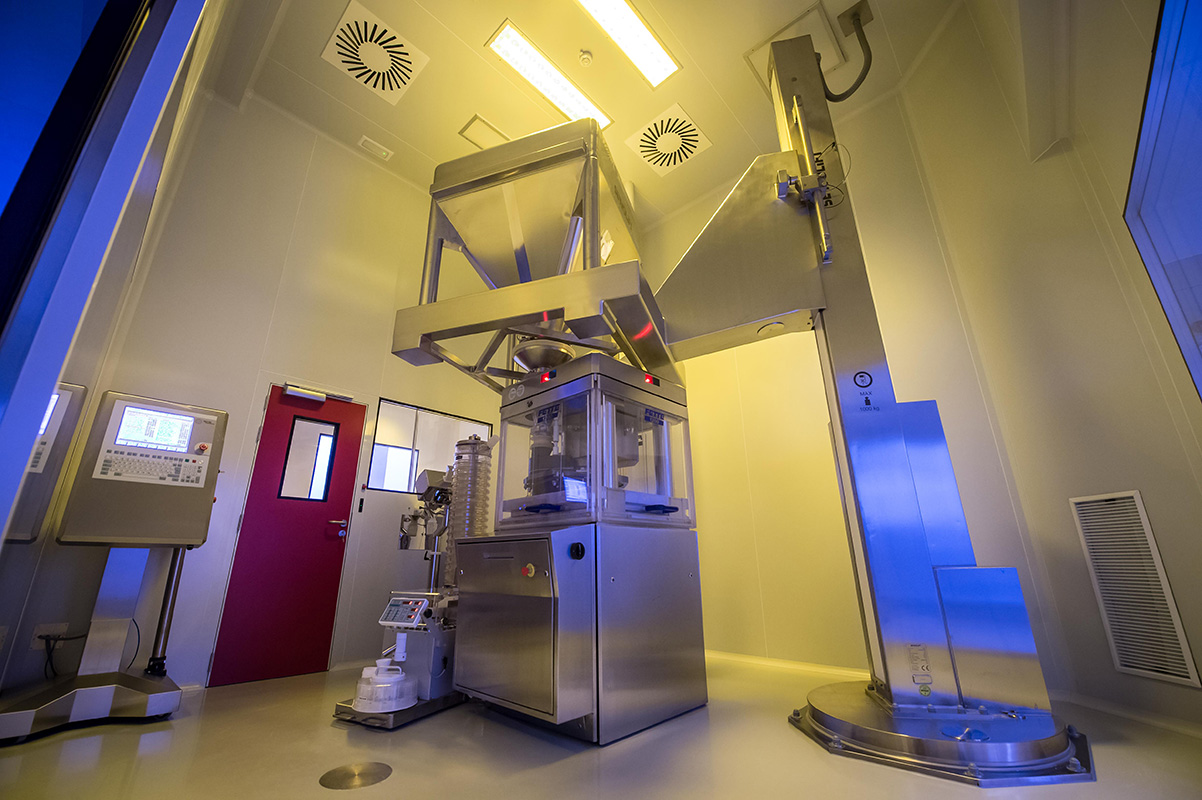
Oral Solids
Production
Compression capabilities include several medium and high speed compressing machines for both single and double layer formulations.
Compressors are fed vertically in a closed loop increasing efficiency and reducing risk of contamination.
In-process control at this stage is largely automated. This ensures a reliable process and stable production flow that travels in a closed loop to bulk IBCs through dedusting and metal detection units.
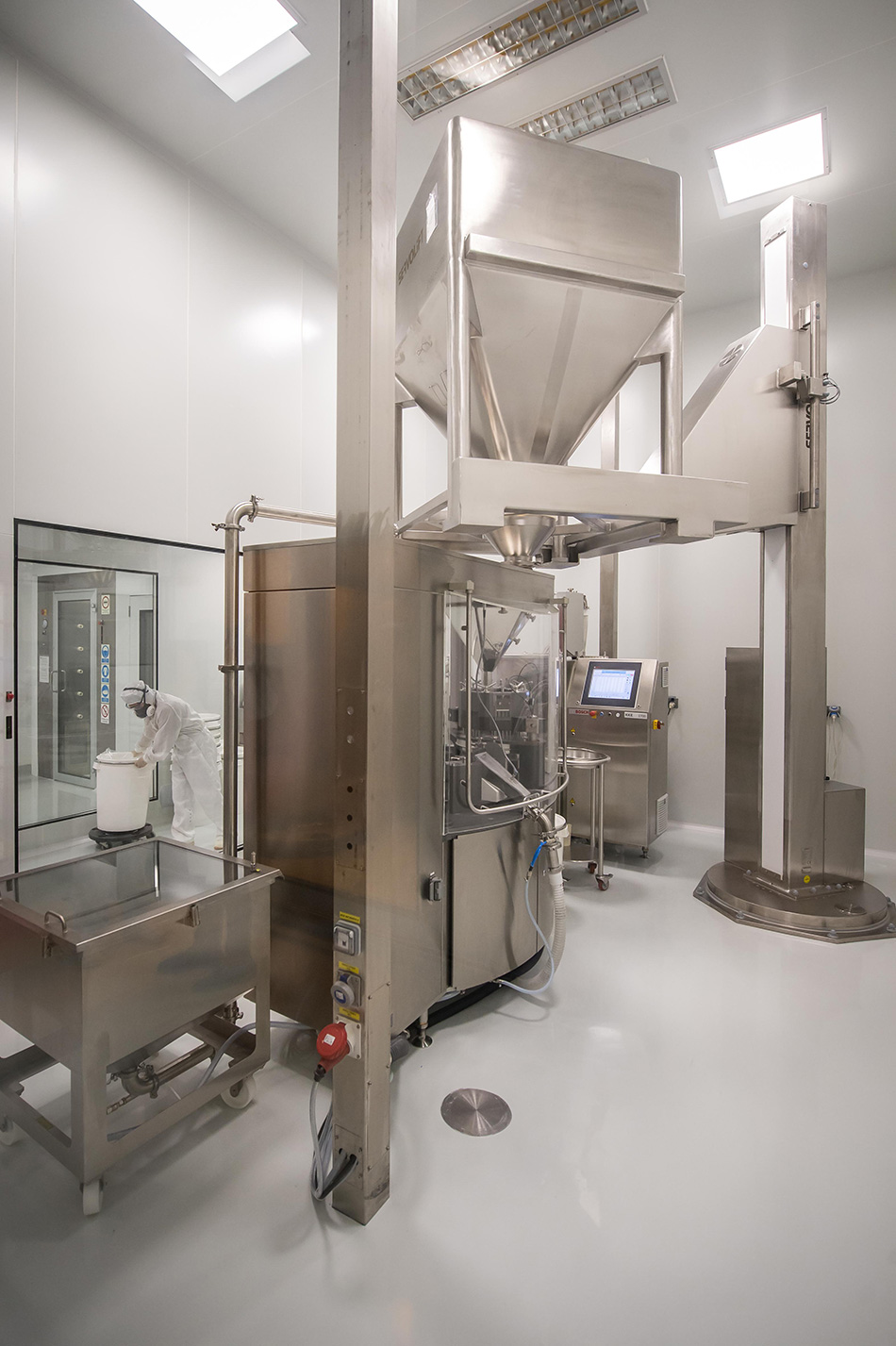
Oral Solids
Production
Hard gelatine capsules are filled in state-of-the-art equipment equipped with a 100% production weight control scale.
The coating of tablets takes place in automatic perforated drum coating machines, ranging from 150 to 500 litres.
These units operate according to automatic formulations, both in production and washing cycles (Work-in-Progress - WIP).
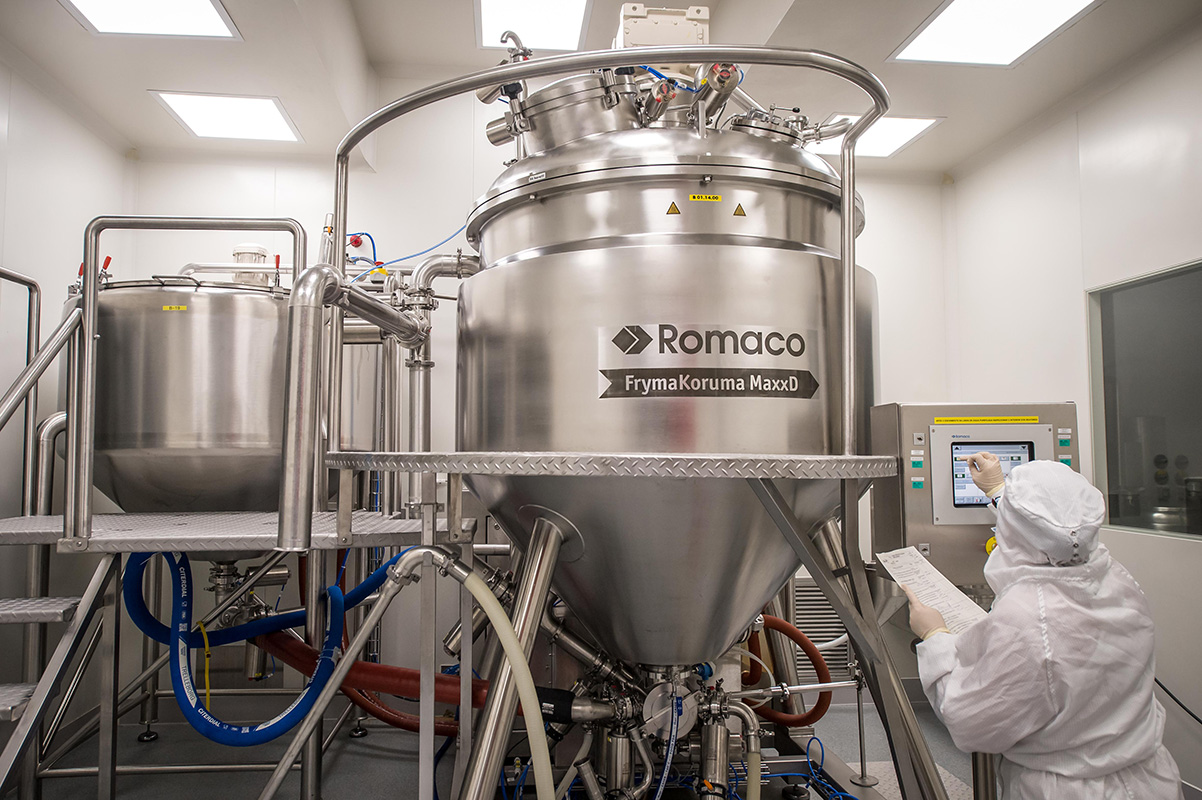
Production of non-sterile liquids and semi-solids
The production areas for liquids and semi-solids (creams and pastes) are equipped with a set of production equipment with volumes typically ranging from 250 to 2,000 litres.
Depending on whether they are dedicated to oral pharmaceutical products, topical application or supplements/ dermocosmetics, the levels of sophistication and automation of our technological solutions are comprehensive.
At its limits, the industrial unit has advanced production reactors equipped with integrated weighing cells, purified water flow meters, as well as automation and reporting of production and washing (W.I.P.) cycles, ensuring the highest standards of quality and safety.
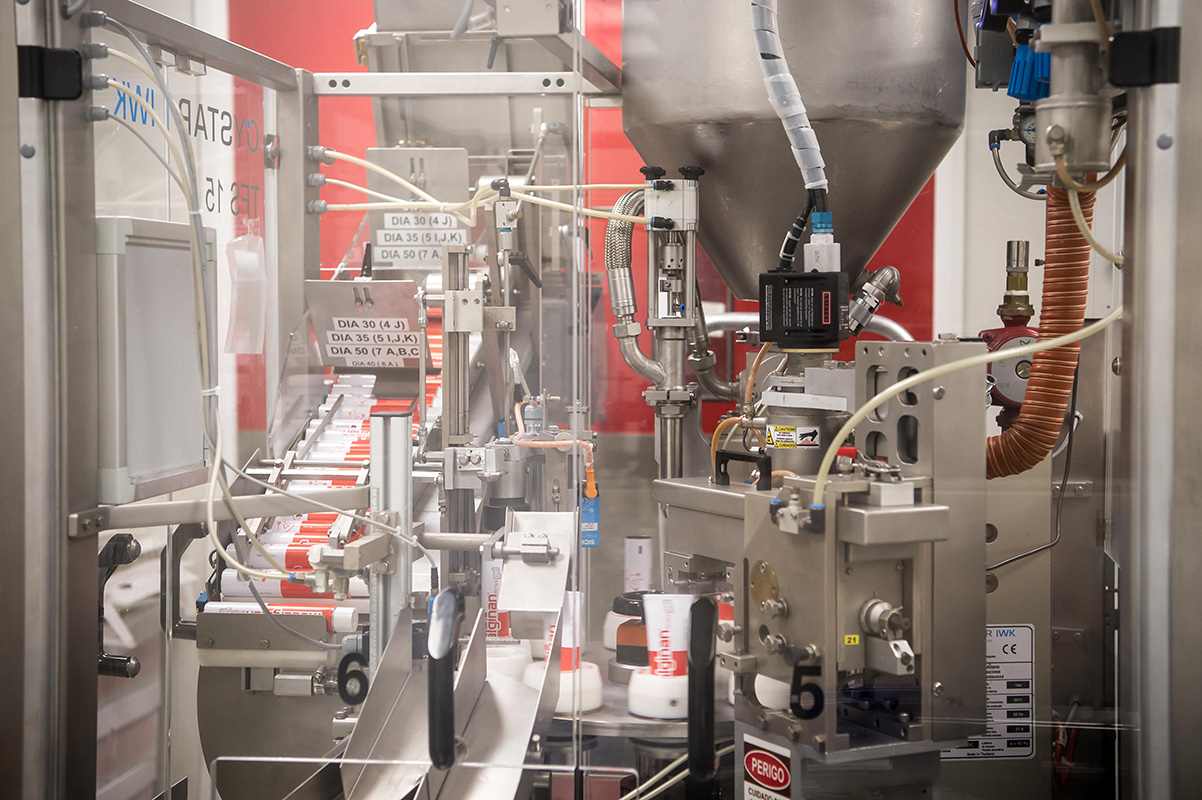
Production of non-sterile liquids and semi-solids
Moreover, regarding filling and packaging equipment, technologies aimed at achieving the highest standards of quality and in-process control are also incorporated, with packaging lines on in-line weighing stations. These include visual inspection systems to ensure the presence of items or the marking of variable data, the placing of tamper-proof seals or the marking of the unique identifier (counterfeit directive), if applicable.